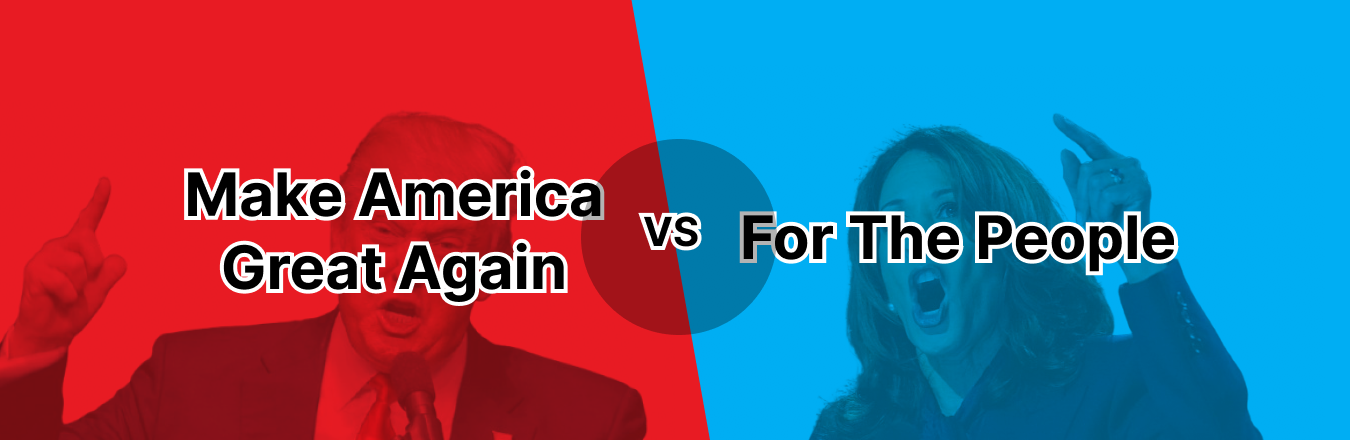
Simon Sinek is right - start with 'why', here's why
A brief description of the post that will appear in previews and social shares.
Read More →Hi Friends,
I'm Walt and I am a creative engineer. I build cool engineering projects, promote them and share the story here on my blog. Join me on my journey.
A brief description of the post that will appear in previews and social shares.
Read More →I just finished reading another book about marketing. The book focused on content marketing. Here are my notes and impressions.
Read More →3 techniques that have helped me a lot in choosing a direction when there's not a right answer.
Read More →Building a consulting company landing page from scratch using AI (Cursor)
Read More →In which an engineer (me) tries to understand "marketing" and how to "do" it. Also, a plan of action for future blog posts.
Read More →